Difference between revisions of "Handpumps"
(→Acknowledgements) |
(→Construction, operations and maintenance) |
||
Line 79: | Line 79: | ||
==Construction, operations and maintenance== | ==Construction, operations and maintenance== | ||
'''General advice on cement''': A common cause of cracks in structures and linings (e.g. in tanks, dams, waterways, wells) is errors in mixing and applying the cement. First of all, it is important that only pure ingredients are used: clean water, clean sand, clean rocks. The materials have to be mixed very thoroughly. Secondly, the amount of water during mixing needs to minimal: the concrete or cement needs to be just workable, on the dry side even, and not fluid. Thirdly, it is essential that during curing the cement or concrete is kept moist at all times, for at least a week. Structures should be covered with plastic, large leaves or other materials during the curing period, and kept wet regularly. | '''General advice on cement''': A common cause of cracks in structures and linings (e.g. in tanks, dams, waterways, wells) is errors in mixing and applying the cement. First of all, it is important that only pure ingredients are used: clean water, clean sand, clean rocks. The materials have to be mixed very thoroughly. Secondly, the amount of water during mixing needs to minimal: the concrete or cement needs to be just workable, on the dry side even, and not fluid. Thirdly, it is essential that during curing the cement or concrete is kept moist at all times, for at least a week. Structures should be covered with plastic, large leaves or other materials during the curing period, and kept wet regularly. | ||
− | |||
====Maintenance==== | ====Maintenance==== |
Revision as of 07:23, 2 November 2012
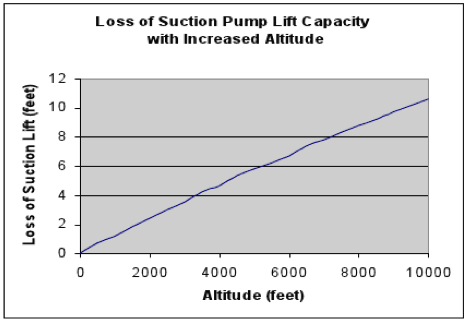
Many different kinds of handpumps are frequently installed on hand-dug wells and boreholes in rural areas, including many drought-prone areas. They facilitate a contamination-free method to extract water. Most pumps are positive displacement pumps and have reciprocating pistons or plungers. There are suction pumps, low lift pumps, direct action pumps, intermediate life pumps, and high lift pumps. For details on these types, look them up in Technology notes: Handpumps (by WaterAid).
Contents
Reciprocating handpumps
The majority of handpump types used worldwide belong to the group of reciprocating pumps. The water is lifted by a piston that is raised and lowered inside a cylinder that has a footvalve. The piston (or plunger) is moved by a pump rod connected directly to a T-handle or a lever handle at the pump head. In some pump types, a flywheel with crankshaft is used to create the reciprocating movement of the piston.
Included in the group of reciprocating handpumps are:
a) suction pumps
b) direct action pumps
c) lever action pumps
The function of the reciprocating pumps is based on the principle that water flows from areas of high pressure to areas of low pressure. The reciprocating pump creates an area of sufficiently low pressure above the body of water, causing it to flow upward.
Suction pumps
In a suction pump, the cylinder is above the water table, usually near the top of the pump head. The rising main extends below the water table. When the pump is operated, during the upwards stroke it appears that water gets “sucked up” through the rising main into the cylinder. In fact, the atmospheric pressure forces the water into the area of low pressure underneath the piston. The theoretical limit to which the atmospheric pressure can push up water is 10 metres (m). In practice, suction pumps can be used to lift water up to about 7 or 8 m.
A suction pump needs to be full of water before it can be operated. That means the pump needs to be primed: water is poured into the pump head by the operator. This is necessary every time the pump is emptied by a leaking footvalve (in practice all footvalves leak a little, especially in inexpensive suction pumps – so the pump may need to be primed every morning, or even several times a day). Thus, the danger exists that the well can be contaminated through polluted water used for priming.
The advantage of suction pumps is that the cylinder is normally above ground, and thus easily accessible. Maintenance involves replacement of seals and valves, operations that can be easily performed with few tools.
Examples of suction pumps include: No. 6 pump, Rope pump, Rower pump, Treadle pump, Super MoneyMaker pump, and MoneyMaker hip pump.
Direct Action handpump
Direct action handpumps are usually made of PVC and other plastics, and are installed on boreholes of limited depth. A plunger is attached to the lower end of a pump rod, beneath the groundwater level. The user moves the pump rod in an up-and-down motion, using a T-bar handle. On the up-stroke, the plunger lifts water into the rising main, and replacement water is drawn into the cylinder through the foot valve. On the downstroke, the foot valve closes, and water passes through a one-way valve in the plunger and is lifted on the next upstroke.
Because direct action handpumps have no mechanical advantage, such as the lever or fly-wheel of a deep-well handpump, direct action pumps can only be used to depths from which an individual can physically lift the column of water (about 12 m). However, the mechanical simplicity, low cost and lightweight construction makes these pumps well equipped to meet O&M objectives at the village level.
The pump is operated by moving a handle up and down. As the plunger is located underwater, no priming is needed. Adults, and even children, can pump the water, although if the water table is further than 5 m deep, this may be difficult for children. The pump stand and site must be kept clean.
Specifications:
- Range of depth: 0–12 m.
- Yield: 0.25–0.42 litres/s at 12 m depth.
- Area of use: Rural and low-income periurban areas, where groundwater tables are within 12m of the surface.
Examples of the Direct Action handpump: Tara pump, Malda pump, Nira AF-85 pump, Canzee pump, EMAS pump, and the PVC pumps has a direct action version.
Lever Action handpump
Most deep-well handpumps are of the lever action type. The increased length of the water column in deep boreholes requires more effort to draw water and the lever of the handle makes the operation easier. Besides the conventional handle, there are also pump designs, which use a flywheel to operate a crankshaft for transforming the rotation into an up-and-down movement.
Lever action pumps consist of:
1. above-ground components like pump head, pump stand and handle, which are usually made of welded mild steel components, preferably with a corrosion protection of hotdip-galvanized zinc layer.
2. down-the-hole components like rising main, pump rods with plunger, cylinder and footvalve.
The configuration of the down-the-hole components can include an open-top cylinder. The plunger and the footvalve can be removed from the cylinder without dismantling the rising main. Or they can feature the conventional configuration with a small diameter rising main and a bigger cylinder diameter, which requires dismantling of the rising main for repairs on plunger or footvalve.
Examples of a Lever Action pump include: Kabul pump, Jibon pump, Walami pump, U3M pump, Afridev pump, Afridev with bottom support, Indus pump, Pamir pump, India Mark 2 and 3, and the Bush pump.
Rotary handpumps
The most commonly used rotary handpumps are the rope pump and the progressive cavity pump (very difficult for local technicians to maintain). Note that although some reciprocating pumps use a circular action mechanism to drive the pistons, they are not categorized as rotary.
Diaphragm pumps
Diaphragm pumps are pumps employing a flexible diaphragm that is expanded and contracted to displace water. The advantages of diaphragm pumps are that they are easy to install, because no heavy mechanical parts are used. They can also be made corrosion-resistant through the use of plastic hoses instead of metallic rising mains.
The disadvantages are that diaphragm pumps need high-quality rubber diaphragms, which are costly to buy and replace, and they have a relatively low efficiency because of the energy needed to expand the diaphragm on every stroke. In addition, the working principle is relatively complex so mechanics and caretakers need to complete comprehensive training programmes.
Example of a diaphragm pump: Vergnet Hydro
Suitable conditions
Overall, it seems sensible that handpumps should be installed only when a viable sustainable handpump option has been shown to work in the area. Depending on pump standardization in country and depth to water table, it is preferable to choose simple technologies that do not need specialist parts and that are repairable locally. The rural poor prefer in any case to have cheaper, shorter-life technologies despite the need to maintain them more frequently.
The ranges over which water can be lifted are grouped in the following categories:
- Suction pumps ____________ 0 - 7 metres
- Low lift pumps ____________ 0 - 15 metres
- Direct action pumps ________ 0 - 15 metres
- Intermediate lift pumps _____ 0 - 25 metres
- High lift pumps ____________ 0 - 45 metres, or more
Trademarks: Volanta, Kardia, Vergnet HPV60/ HPV100, Bluepump
Public Domain conventional lever action: Afridev pump, India Mark 2 and 3, Indus pump, Kabul pump, Pamir pump, Jibon pump, U3M pump, and Walami pump.
Construction, operations and maintenance
General advice on cement: A common cause of cracks in structures and linings (e.g. in tanks, dams, waterways, wells) is errors in mixing and applying the cement. First of all, it is important that only pure ingredients are used: clean water, clean sand, clean rocks. The materials have to be mixed very thoroughly. Secondly, the amount of water during mixing needs to minimal: the concrete or cement needs to be just workable, on the dry side even, and not fluid. Thirdly, it is essential that during curing the cement or concrete is kept moist at all times, for at least a week. Structures should be covered with plastic, large leaves or other materials during the curing period, and kept wet regularly.
Maintenance
Historically, handpump functionality has been negatively affected by numerous issues related to user operation & maintenance, which in turn has resulted in a large percentage of handpumps that do not work. However techniques to improve sustainability of handpump installations are possible. Centralized management of spare parts stock seems to be preferable to private sector supply chains for a variety of reasons related to the difficulties of sustaining handpump spares.
Maintenance of direct action pumps is relatively simple and can be taught to users or caretakers, sometimes within a few hours. For preventive maintenance, usually only one or two people are needed. Daily activities consist of checking the pump performance and the appearance of the water (if it is cloudy with silt, the borehole must be cleaned). Annually, the pump should be taken apart and checked. Small repairs include replacing worn cupseals and washers, straightening bent pump rods, and replacing corroded lock nuts. To carry out major repairs (e.g. a broken pump rod or rising main, cracks in the welding of metal parts), skilled help may be needed. O&M can be organized at community level, and since maintenance is relatively simple, good organization will result in a reliable service.
Potential problems
- Worn washers, plungers and foot valve parts
- Abrasion of the seal on the PVC cylinder and between the pump rod and rising main
- Broken or damaged handles
- The maximum lift is limited to about 12 m.
- The force needed to pump the water may be too great for children, especially if the water table is below 5 m.
The VLOM concept
The term VLOM (Village Level Operation and Maintenance) was coined during the World Bank / UNDP Rural Water Supply Handpumps Project which, from 1981 - 91, considered the availability around the world at that time of handpump technologies and maintenance systems.
A series of performance tests were undertaken involving laboratory testing of 40 types of handpump and field performance monitoring of 2700 handpumps. It was concluded that centralised maintenance systems were the cause of many problems and that village level maintenance was desirable, but only feasible if the design of the pump made it possible.
Initially the VLOM concept was applied to the hardware, with the aim being to develop pumps which were designed to be:
- Easily maintained by a village caretaker, requiring minimal skills and few tools
- Manufactured in-country, primarily to ensure the availability of spare parts
- Robust and reliable under field conditions
- Cost effective
Subsequently, the VLOM concept was extended into software and organisational matters. Thus the "M" in "VLOM" has become "management of maintenance", for the success of a project was generally seen to be dependent on a strong emphasis on village management.
Therefore the following elements were added:
- Choice by the community of when to service pumps
- Choice by the community of who will service pumps
- Direct payment by the community to the caretakers
The application of VLOM principles, when considering pump selection, often involves compromising one principle to take advantage of another. A handpump with a low rate of breakdown might be thought preferable to another with a higher rate. However, a handpump that breaks down monthly, but can be repaired in a few hours by a local caretaker, is preferable to one that breaks down once a year but requires a month for repairs to be completed and needs replacement parts to be imported and skilled technicians to be available.
The Afridev handpump was developed during the course of the project to embody all of the VLOM design principles. Production began in Kenya in 1985 and modifications were made after field trials in Kwale in Southern Kenya.
Improvements continue to be made. SKAT (Swiss Centre for Development Co-operation in Technology and Management) acts as a repository for the design drawings and specifications for the benefit of users and manufacturers of the handpumps.
Costs
Direct Action Handpump - Initial cost: From about US$100 to over $900 (1985 prices). Models suitable for village level O&M cost less than US$150.
Analysis of costs for handpumps: COMPARING SIMPLE PUMP TO OTHER PUMPS, by Simple Pump.
Field experiences
Tests were done on some handpumps that are documented in A Sustainable Technology: Research and Development During Water Supply and Sanitation Decade, by UNDP - World Bank Water and Sanitation Program. Refer to the following pages of this document:
Kenya--The Afridev Handpump p. 80-84.
India - The India Mark II and Mark III (VLOM) Handpumps p. 84-89.
Bangladesh - The Tara Direct-Action Pump p. 89 and 90.
References manuals, videos, and links
- RWSN: Comprehensive information on community handpumps, including manuals and specifications for Afridev, Indian Mark II/III and Tara pumps
- Pumps. Different kinds of pumps. PRACTICA Foundation.
Acknowledgements
- Brikke, François, and Bredero, Maarten. Linking technology choice with operation and maintenance in the context of community water supply and sanitation: A reference document for planners and project staff. World Health Organization and IRC Water and Sanitation Centre. Geneva, Switzerland 2003.
- Szánto, Gábor L. et al. Drinking Water Decision Support Tool. PRACTICA Foundation. 2011.
- CARE Nederland, Desk Study Resilient WASH systems in drought prone areas. October 2010.
- Technology Notes: Handpumps. WaterAid.
- Reynolds, John, A Sustainable Technology: Research and Development During Water Supply and Sanitation Decade. UNDP - World Bank Water and Sanitation Program, 1992.