Riverbed jetted and driven wells
![]() |
![]() |
![]() |
![]() |
![]() |
![]() |
![]() |
![]() |
![]() |
![]() |
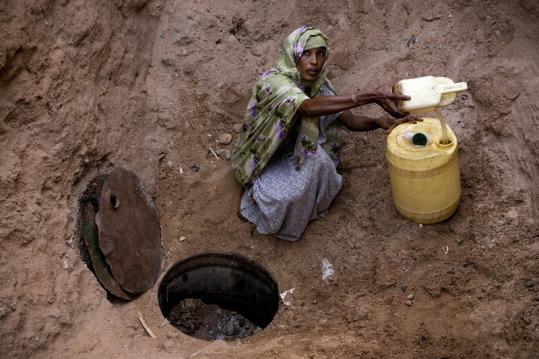
This category includes short small diameter cylindrical screens (slotted or perforated pipes) that are inserted into unconsolidated sediments using water pressure or physical force, usually vertically or obliquely. Digging is not needed in this case.
Suitable conditions
Due to pumping requirements, it is best to site these wells:
- Within 30 metres of the pump location.
- In areas where there are no high banks and where maximum floodwater height is lower than these banks – this is so that suction pumps can still operate (effectively will abstract water between 6 – 7 metres height).
- There should be water remaining in the riverbed throughout the dry season.
Advantages | Disadvantages |
---|---|
- Speed and low cost of construction - High yields possible with small intakes. |
- More difficult to do in sandy sediments that are mixed with clay. - No storage capacity as with large diameter wells. |
Construction, operations and maintenance
The screens and pipework should be ideally 1.5 metres minimum from the riverbed surface. This is so that:
- There is at least a minimum of infiltration that occurs from surface water during the wet season when the river is flooded.
- That there is less chance that the well shaft and pipework will be washed away in a flood event. Sand becomes mobile to a certain depth which differs for different rivers but has been recorded to be normally between 0.66 and 2 metres in seasonal riverbeds.
Screens used can be anywhere from 32 to 200 mm in diameter, and only 0.5 – 1 metre in length. For jetted wellpoints, they are commonly made from plastic. For driven wellpoints, they are made from steel and require wingtips on the pointed end.
Jetting (also known as washboring) is one method of installing a screen into the saturated sand layer. There are various forms of jetting, with various pipe sizes. Key techniques are outlined below:
- About 1,000 litres of water is required, possibly more depending on ease of procedure and size of sediment particles. This water can be brought with a bowser, or can be created using a hole dug into the ground and lined with a plastic sheet.
- A 2” Honda suction pump (600 litres/min) is normally used for both jetting and well testing, although larger capacity pumps will enable deeper jetting but will use more water per minute.
- During the jetting process, water emerges from the end of the jetting pipe and flows upwards to ground level. If the flow of water stops (e.g. water runs out, or to change a pipe), in most circumstances the sand around the jetting pipe/screen will collapse, after which it is impossible to re-start the flow of water to the surface. However, in some cases the hole will remain open – only in these cases can you add another pipe and continue jetting, but otherwise the depth you can install the screen is dependent on the length of jetting that can be done in one go without stopping the pump.
- Digging a large pit to the water table is advantageous since:
- In collapsing sands, you can jet to the base of the pit, after which you can glue extra pipes onto the screen to reach ground level, so that a deeper well is achieved.
- The chance of losing the water column is minimized due to less pressure head that the water must overcome in order to flow to the surface. With higher pressure heads (i.e. more distance from water level in ground to ground level), the water is more likely to choose the path of least resistance, which at some point will be to go into the aquifer rather than come to the surface. In such a case where you lose the water column in collapsing sands, the well will be finished at that depth.
- A screen can have a ball valve at the end – in this case, the jetting pipe and screen are made from the same piece. Alternatively the screen can be separate from the jetting pipe, where the jetting pipe creates the hole and then is removed once the screen is installed to required depth. If a screen with valve is chosen, care should be taken if installing handpumps as the ball valve has a tendency to open over time letting in sand.
- Flow velocity around the screen should be maximized. This can be done by adding a layer of perforated drainage pipe around the screen, followed by geotextile. Additionally, a gravel pack should be created around the screen. This can be done by:
- Throttling the pump speed down once the screen is at the required depth – this will remove fines while allowing coarse sediments to settle around the screen depth.
- For sand rivers that have a significant clay content, permeability in the riverbed will be low, and yields will also be low. Increased flow velocity into the well can be created by making a large gravel pack around the well shaft – this gravel pack consists of aggregate and stones (rather than the traditional type of small diameter gravel pack used in boreholes).
Extracting water can be done with handpump or mechanical pump. Handpump cylinder will need to physically be able to fit inside the screen that has been installed.
Manuals, videos and links
- Well revival effort sees many other benefits A community drive to revive wells in Mokhla talab near Udaipur results in water security for longer periods of time as well as making leaders out of women.
- Experiments with 'community wells' Mobilized farmers in Dhule, Maharashtra, show how communities can use groundwater as a common resource in an organised and collective manner.
Acknowledgements
- CARE Nederland, Desk Study: Resilient WASH systems in drought-prone areas October 2010.