Hydraulic Ram pump
![]() |
![]() |
![]() |
![]() |
![]() |
![]() |
![]() |
![]() |
![]() |
![]() |
![]() |
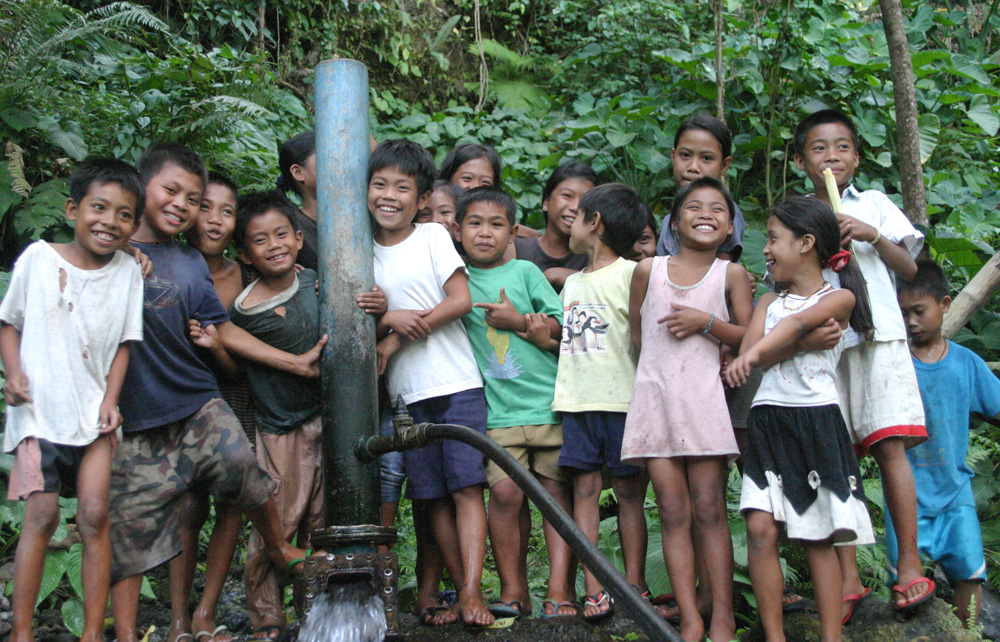
A hydraulic ram pump is a water pump powered by water with a height difference. In areas where natural flows exist with a height difference of the water over a small distance, hydraulic ram pumps can be used to transport water to higher grounds without using electricity or fuel. The hydraulic ram uses the water hammer effect to develop pressure that allows a portion of the input water that powers the pump to be lifted to a point higher than where the water originally started. Apart from the kinetic energy of the water, no other source of power is needed.
The hydraulic ram pump was invented in 1772 and widely used in the 19th century, but was side-tracked by the advent of the coal-powered steam engine and later by diesel powered pumps. In recent years the hydraulic ram pump has seen a renewed interest, because it is powered by sustainable energy, and can be produced locally.
Contents
Suitable conditions
A hydraulic ram pump is powered by a body of water flowing downhill with a height difference. A general rule of thumb is that the water can be pumped 30 times as high as the available drive head (the height difference of the water driving the pump). So a head of 1 m can be used to pump up water to ~30m, while a 7 m head can pump water up to 210 m.
The capacity of a hydraulic ram depends on the scale of the pump, which is often measured in the diameter of the tube delivering the water to the pump. Pumps exist in the range 1" up to 5".
With height difference, the actual difference in vertical height is meant, not the length measured along the slope.
Advantages | Disadvantages |
---|---|
- Uses renewable energy sources. - If properly designed, can be produced and maintained locally. |
- Water with height difference is needed |
Construction, operations and maintenance
A hydraulic ram has only two moving parts, a spring or weight loaded "waste" valve sometimes known as the "clack" valve and a "delivery" check valve, making it cheap to build, easy to maintain, and very reliable. In addition, there is a drive pipe supplying water from an elevated source, and a delivery pipe, taking a portion of the water that comes through the drive pipe to an elevation higher than the source.
The optimum length of the drive pipe is five-to-twelve times the vertical distance between the source and the pump, or 500-to-1000 times the diameter of the delivery pipe, whichever is less. This length of drive pipe typically results in a period between pulses of one-to-two seconds. A typical efficiency is 60%, but up to 80% is possible. The drive pipe is ordinarily straight but can be curved or even wound in a spiral. The main requirement is that it be inelastic, strong, and rigid; otherwise, it would greatly diminish the efficiency.
A simplified hydraulic ram is shown in the figure. Initially, the waste valve [4] is open, and the delivery valve [5] is closed. The water in the drive pipe [1] starts to flow under the force of gravity and picks up speed and kinetic energy until it forces the waste valve closed. The momentum of the water flow in the supply pipe against the now closed waste valve causes a water hammer that raises the pressure in the pump, opens the delivery valve [5], and forces some water to flow into the delivery pipe [3].
Because this water is being forced uphill through the delivery pipe farther than it is falling downhill from the source, the flow slows; when the flow reverses, the delivery check valve closes. If all water flow has stopped, the loaded waste valve reopens against the now static head, which allows the process to begin again.
A pressure vessel containing air [6] cushions the hydraulic pressure shock when the waste valve closes, and it also improves the pumping efficiency by allowing a more constant flow through the delivery pipe. Although, in theory, the pump could work without it, the efficiency would drop drastically and the pump would be subject to extraordinary stresses that would shorten its life considerably. One problem is that the pressurized air will gradually dissolve into the water until none remains. A simple solution to this problem is to introduce a so-called snifting valve that automatically inserts a small bubble of air with each pump cycle.[5]
Maintenance
Some common operational problems are intrusion of air into the drive pipe, blockage of the intake or valves with debris, knocking due to having too little air in the pressure vessel, freezing in winter and bursting of the delivery pipe if its output is blocked or not pressure relieved.
Field experiences
This article describes the impact the introduction of the hydraulic ram has had in the Philippines.
Akvo RSR Projects
The following project(s) utilize a hydraulic ram pump.
![]() MWA-LAP: Nicaragua |
Manuals, videos and links
hydraulic ram, 16min. |
by AID Foundation, Philippines |
Ram pumps in Afghanistan |
by R.A. Initiatives |
- Hydraulic Ram article on Wikipedia
- Article on the AID Foundation hydraulic ram, winner of the Ashden Award in 2007
- Hydraulic ram pumps, Practical Action.
- Several in-depth articles on the function and construction of hydraulic rams, including detailed drawings of a low-cost and tested design. Development Technology Unit (DTU), University of Warwick, UK
- Low cost self-made pump, Clemson University.
- Another low-tech pump design, Judy of the Woods.
- Akvo solution of the week 12
Acknowledgements
- This article is adapted from the Wikipedia article Hydraulic Ram