Rope pump
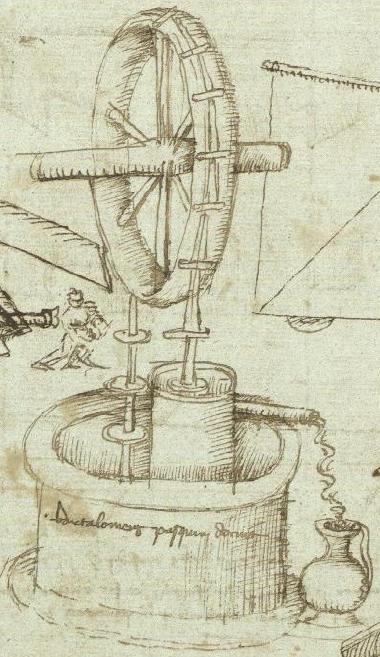
The Rope Pump is a highly efficient, modern and low cost pump and one of the few designs that can truly be operated and maintained totally at a village level. There are various modern developments of the ancient design but the basic design of all pumps is a continuous loop of rope with pistons (or plastic washers) attached to it, the rope passes up through a plastic pipe with only a small clearance, thus allowing the pistons to push the water up and out of the top of the pipe. Rope pumps have proven highly successful and there are hundreds of thousands of pumps in use world wide and used for anything from community adn domestic water supply to irrigation and cattle watering. For wells down to 35 m, rope pumps are often five times cheaper and more sustainable than standard piston pumps. Rope pumps can be powered by hand, bicycle, motor, horse, or wind power.
Contents
History and social context
Origins
The almost intuitive design is known by many other names including the paternoster (after the beaded prayer chain it resembles), liberation or rope-and-washer pump. It is a relatively recent development of the ancient chain-and-washer pump. Evidence of the chain-and-washer pump dates back as far as two thousand years, to feudal China 2. The earliest report of the design in the west is cited 3 as that illustrated by the Sienese early renaissance engineer, Tacolla, circa 1433 4, a copy of which is given in the figure to the right 5. In the 1970 and 80s the basic design was developed by numerous individuals, the most prominent of which were Alberts 6, Haemhouts 7 and Lambert 8. and Thorpe. They applied the simple design as a tool aimed at economic and social development. They took advantage of low cost and versatile modern plastics to produce the modern rope-pump design.
Recent Experience
Because of its low cost, the pump is also popular for domestic use. A survey among 5,025 rural families in Nicaragua indicates that a rope pump increases income, even if used for domestic purposes only. Families with a pump earn US$ 220 per year more than families without a pump. In Nicaragua the pumps are now being produced commercially by 20 workshops.
Different models of Rope pumps were introduced in Africa. This introduction has not always been successful: in one projects over 80% of the pumps did NOT work after one year! However, with the "right" models and the "right" user training, up to 90% remain in operation in Africa, as the Victory model in Ghana and the Elephant model in Zimbabwe have proved.
Suitable conditions
A rope pump can be used to draw water from wells or boreholes. Applications include communal wells, households, irrigation, and cattle watering.
One person can draw water up to 35 m, two persons can pump to 60m (using a second crank). A rope pump can be driven by hand, windmill, motor, bicycle, and animals. A rope pump can pump 40 litres / min from 10 meters depth.
Some 70,000 rope pumps are in use in Nicaragua, 20,000 in Mexico, Honduras, Guatemala, El Salvador, Ethiopia, Ghana, Senegal, Tanzania, Zambia, Mozambique, Zimbabwe, Cambodia, India, Vietnam, and others. In total, the Rope pump is used in over 30 countries.
The pump can be used by single families, or up to 20 families (100 people).
Advantages | Disadvantages/limitations |
---|---|
- Significantly cheaper (up to 5 times) than piston pumps. - If made well, one pump can supply up to 250 people as experiences in Nicaragua, Ghana and other countries indicate. However, suggested use is for maximum of 20 families (100 people) |
- The rope pump is easy to copy, but bad copying (materials, construction) leads to early break down.
- Lack of maintenance and installation errors, can lead to early wearing out or breakage of pump parts |
Technical specification
With different depths, different sizes of pump pipes are needed, otherwise the pumping becomes to heavy. See manuals on websites
of Practica Foundation and Connect International.
Many different types of rope pump exist, powered by hand, bicycle, wind, horse, etc.
Similar to piston pumps, a cement slab and a good soak away are needed to avoid splash water becoming a cause for pollution.
Design
- Pumping depth (Lift): 0 to 30m
- Cylinder diameter: 28 mm to 42 mm, depending on depth
- Piston: Plastic pistons spaced at 1 m
- Yield: (75 watt input, at 5 m head) ~ 4.5 m³/hour
- Population/field area served: 0.25 hectare
- Type of well: dug well or borehole
Manufacturing and Materials
The rope pump can be produced with locally available standard materials and local skills, such as an artisan workshop.
The frame is welded from mild steel. The handle axle is a mild steel pipe (some design use bearings, either ball bearings or wooden bearings, other employ a steel bushing. The pulley wheel is assembled by fitting the cut-off sides of a tyre on a rim, which generates a nice 'v' shape which provides good traction on the rope. The ropes are made of Polyethylene, Polypropylene, or Polyamide fibres varying from Ø 4 to Ø 8 mm. Natural fibres are not suitable, as they will lengthen when wet, and degrade too fast. The pistons are injection moulded plastic with no seal. The rising main are PVC pipes ranging from 20-50mm diameter (depending on lift). The guide box can be made of concrete with a ceramic insert (some designs use cast in glass bottles), or made of wood with a pvc lining.
Installation
The installation of the Rope pump is easy and does not need any lifting equipment or special tools. The pumps are generally installed in dug wells but also versions that fit into boreholes are available.
Maintenance
One of the main strengths of the rope pump is that all maintenance is relatively simple and can easily and genuinely be done at village level. All spare parts can, like the whole pump, be manufactured in any small town with only the most basic welding machine, other standard hand tools and a basic supply of standard items like PVC pipe, GS pipe and round bar. The most frequent repairs are simple and consist mainly of repairing the rope or handle. Although easy and simple to maintain it is important the user is instructed in why and how to maintain and repair their pump. Evaluations show that rope pumps on communal wells can be maintained by the users under certain conditions. On pumps shared amongst large groups one of the main conditions is a very high level of community coherence and responsibility. If the rope pump technology is introduced properly, like often is the case with the Zimbabwe Elephant Rope pump, up to 90% of rope pumps remain operational, even after many years.
Efficiency & Theoretical Models
Motorized rope pumps
Most common diesel and petrol pumps are suction pumps that can pump from shallow wells down to 7 m. deep. Pumping from deeper wells requires generator pump sets or long-shaft diesel pumps costing US$ 800 or more. Where there is electricity, submersible pumps can be used but many small farmers do not have electricity.
Motorised rope pumps can pump from deep wells, up to 60m.9 This model combines a rope pump with an electric motor or petrol engine. Pump parts and other elements of the structure can be produced in local workshops, the engines are often imported.
If combined with a locally available small petrol engine the cost of a motorised deep-well pump can be US$ 450. This is far cheaper then long-shaft diesel pumps or submersible pumps and this cost can even be less when Chinese engines are used.
Similar to hand rope pumps, the pump part can be maintained and repaired by the users. The motorised rope pump is being tested in Columbia and Nicaragua.
Cost
- The Rope Pump costs between US$ 30-150 depending on model, location of production, and cost of materials and labour.
- Cost of introduction: between US$ 10,000-30,000 per project, including 20 pumps, engineering and hands-on training.
- Rural water programme: US$ 150,000-200,000 per project, including 1,000 pumps, start up of production facility and hands-on training.
Country experiences
In 2008, rope pumps are used in over 30 countries. Below the experiences in Nicaragua, Zimbabwe and Ghana are listed.
Nicaragua Some 70.000 rope pumps have been installed since 1990. The shift from imported piston pumps of 600$ to locally produced rope pumps of 70$ has doubled rural water supply in ten years, much faster than countries that apply piston pumps. Users do the maintenance and over 95% of the pumps remain in operation. The rope pump has been adopted as the standard water pump by the government.
Zimbabwe A rope pump model called the Elephant Pump was introduced by the organisation Pump Aid in 1990. The main difference with the traditional rope pump is the solid round structure around the wheel, to protect the well and to avoid splashing. Now some 3,000 pumps serve 950,000 people and some 95% of the pumps are working. Many more pumps are planned to be installed before 2015 and if this can be realized, this will reach 3 million more people.
Ghana The first experiences with rope pumps in Ghana were discouraging. In a World Bank funded project, 80% did not function after one year because of lack of user involvement and production errors. After improvements some 1.600 pumps were installed.
Malawi, Blantyre trials Several rope pumps were introduced in order to provide a better alternative for the Afridev Community handpump, which is the standard handpump in Malawi. The Afridev is not popular due to many breakdowns and not available spare parts, especially in the more remote areas. However, the rope pumps also broke down many times, sometimes several times per month, due to the high number of users and was therefor not considered by the users as a good alternative for a community pump, although repairs were possible. Another disadvantage mentionned was that children found it difficult to pump and sometimes got hurt when the handle security break system was not functioning (in that case the handle turns back with a high speed due to the weight of the water in the riser pipe). The communities now prefer a more reliable handpump than the Afridev, with less need for spares.
Mozambique As in Malawi, the rope pump was seen as a viable alternative to the Afridev which is generally the official pump of choice. WaterAid had first introduced a bucket and windlass system in the Niassa provice as an alternative due to the high failure rate of Afridev pumps, but the Mozambican government refused to accept these as official community water supplies. WaterAid, in partnership with the Swiss Agency for Development Cooperation (SDC), UNICEF, CARE and the Government of Mozambique, therefore began a lengthy process of piloting a robust community rope pump, first relying on support from Bombas de Mecate in Nicaragua, but later adapting the design from Madagascar. The new model meets a number of key well protection and water quality criteria set down by the development team. Three manufacturers are now in operation in three provinces and through a process of skill sharing improvements have been made to the design resulting in a robust high quality model. A manufacturing standard has also been produced with the help of SKAT. The final stages of this process are currently underway which include the final approval of the pump as well as the licensing of the manufacturers by the Governments standards laboratory.
There are now more than 300 rope pumps installed across three provinces (Niassa, Cabo Delgado and Zambezia)and in Niassa particularly WaterAid funded projects continues to offer communities a choice of either the Rope Pump of the Afridev. In addition the installed pumps are monitored twice per year in order to better understand the pumps sustainability.
Apart from this initiative, PumpAid has also been active in the Chimoio province installing Elephant Pumps which are also rope pumps.
Please see the external links below for further information.
Burkina Faso WaterAid in Burkina Faso is also currently developing a rope pump model suitable to local conditions. This project has resulted in a renewed understanding across WaterAid of the need to ensure that rope pumps destined for community water supplies require high quality manufacturing and installation techniques in order to improve their sustainability. WaterAid now intends to renew its efforts across the organisation to improving the quality of rope pumps in countries where this is supported. A training course for manufacturers from Burkina Faso, Ghana, Mali, Zambia and Malawi was held in early 2010 as part of this process.
A recent interesting development in Burkina Faso has been the re-design of the bottom guide box to include a non-return valve (foot valve) thereby ensuring that water is immediately available from the first turn of the pump handle. This is currently being piloted on a few pumps.
Manuals
- Rope Pump production manual, produced by PRACTICA and ETC Foundation. It has 86 pages and contains detailed instructions.
- Construction manual Connect International.
Movies
- Rope pumps around the world (Connect International, Netherlands, 2008)
- Small scale irrigation with a rope pump, Zambia (Connect International, Netherlands, 2008)
- Hand drilled borehole and rope pump in Tanzania (Connect International, Netherlands, 2008)
- Windmill powered rope pump in Nicaragua (S.J. Batchelor, 1999)
- Rope Pump animation (Resource Development International Cambodia, RDI)
- Motorized rope pump on platform in Ethiopia, used to fill an overhead tank
- Motorized rope pump in Burkina Faso, used for smalls scale irrigation.
- Rope pump documentary part 1
- Rope pump documentary part 2
External links
- www.ropepumps.org website
- Rope pumps: out-perform conventional handpumps on most counts in Ghana test. Article on IRC.
- Rope pump: local production and installation capacity being developed in Senegal. Article on IRC.
- Overview of community handpumps at the RWSN website
- Low-cost pump alternatives for rural communities in Honduras (rope- and EMAS pumps), SKAT website
- Pump Aid works in Malawi and Zimbambwe with the Elephant pump, a kind of rope pump.
- www.ropepump.com
- Ideas at Work, Cambodia
- Rope Pump - WaterAid in Mozambique
- Rope pump article at Appropedia
- Akvo solution of the week 7
- Akvo solution of the week 9
- 'Low Cost Handpumps' RWSN Field Note 2011-3
References
- ↑ Weisbaden, Ludwig, ed. et al. Facsimile of De Ingeineis, Liber Primus Leonis, Liber Secundis Draconis, Addenda [online]. Germany: Satz Und Druck, 1984. Available at: http://digital.library.cornell.edu/k/kmoddl/pdf/037_001.pdf [April 2009]
- ↑ Fraenkel, Peter, and Thake, Jeremy. Water Lifting Devices, A handbook for users and choosers, 3rd ed. UK, Rugby: Intermediate Technology Publications Ltd, 2006.
- ↑ Olsen, J. P. Greek & Roman Mechanical Water-Lifting Devices: The History of a Technology. Toronto, Canada: University of Toronto Press, 1984.
- ↑ Tacolla, Mariano. De Ingeineis, Liber Primus Leonis, Liber Secundis Draconis, Addenda. c. 1433, folio 80.
- ↑ Weisbaden, Ludwig, ed. et al. Facsimile of De Ingeineis, Liber Primus Leonis, Liber Secundis Draconis, Addenda [online]. Germany: Satz Und Druck, 1984. Available at: http://digital.library.cornell.edu/k/kmoddl/pdf/037_001.pdf [April 2009]
- ↑ Alberts, J. H. The rope-pump - an example of technology transfer. Waterlines, January 2004, Vol. 22 (3), 22-25.
- ↑ Sandiford, Peter, et al. The Nicaraguan Rope-pump. Waterlines, January 1993, Vol. 11 (3).
- ↑ Lambert, R. A. How to build a rope-and-washer pump. London: Intermediate Technology Design Group, 1990.
- ↑ Information on Motorized rope pumps on the website of Practica Foundation
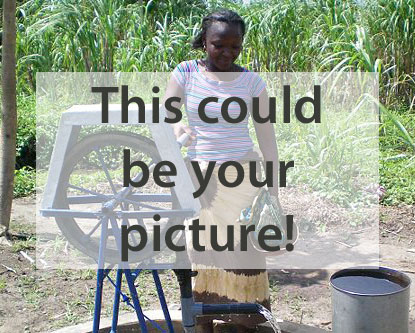
|