Concrete production and drought
From Akvopedia
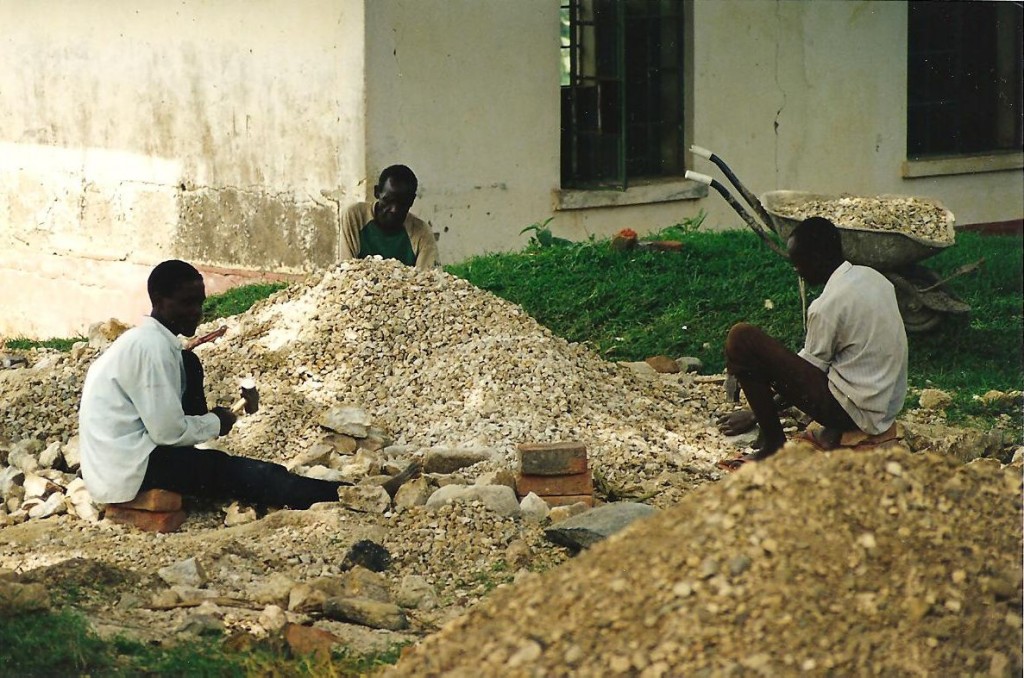
Breaking stones to make aggregate for concrete in Uganda, East Africa. Polishing Peanuts blog.
Poor construction techniques are to blame for many leaking water structures, which in turn affects water availability. Key construction issues such as the making of concrete, correct construction of stone masonry, as well as the issue of pipes passing through water-bearing structures. This section focuses on concrete making. Proper techniques are often bypassed or shortened, which increases the risk of failure and reduces the life of the structures. This is especially true in many drought-prone areas that have dry climates and where water is at a premium, since it affects the essential curing process.
Construction, operations and maintenance
All dry ingredients should be mixed first before adding water.
- Use the correct ratios for different applications – refer to relevant tables. A field method to check if contractors have used the correct ratio is to take some of the wet mix, put it into a transparent bottle and shake up with some water – the cement fraction should settle out on top when it is left to stand, giving an indication of the cement fraction.
- Add only the very minimum amount of water for workability – this is one of the most important aspects to making strong concrete. The amount of water needed for the hydration process when mixing concrete is a lot less than what is normally added to mixtures in the field, where additional water is needed to increase workability of the concrete. The point is that the less water used, the better, since if too much water is used, the concrete will become weaker. Any excess water not used in hydration will remain in the pores – when this water evaporates, the pores remain – the more water added, the bigger the pores and the weaker the final product. Admixtures can be added to the concrete mix in order to reduce the amount of water needed. Superplasticizers work best by reducing the amount of water that needs to be added when mixing concrete, which results in 35% less shrinkage. The resulting end material is stronger and can reduce the amount of micro cracks in mortar by half compared to normal mortar while resulting in 76% fewer leaks. The amount of plasticizer to be added should not be greater than 2% of the dry material weight. A plasticizer that can be used that is possibly available is household washing up liquid. In hot climates though, more research is needed in the field application of plasticizers, since the reduction of water used (and increased strength of product) may not be that great due to more water needed to prevent drying out between mixing and application.
- Type of water used should be as pure as possible.
- Don’t use weathered rock for concrete aggregate. For the best concrete it is best to use a fresh rock aggregate such as crushed granite of gneiss or well-washed river gravel. With the latter the river has removed the weak pieces.
- Use clean gravel – impurities will weaken the concrete.
- Use aggregate (gravel) of 5-20mm for non-porous concrete and 5-10mm for porous concrete. Aggregate can be graded using 2 locally-made sieves of 5mm and 20mm – discard any aggregate that remains on the 20mm sieve or that falls through the 5mm sieve. The reasons for having a maximum size is to do with workability, but also that the maximum size is not greater than the “cover” of concrete over a reinforcing bar – if a stone would span the distance from outer edge to reinforcement, this can become a zone of weathering where water can get in to corrode the reinforcement.
- Reinforce lower side of flat slabs as concrete does not work well under tension. Reinforcement can be avoided if making dome shape structures (e.g. cover to rainwater tank, or dome latrine slab).
- Spacing of reinforcement bars depends on the slab span, thickness and type of reinforcement used – refer to relevant tables.
- Place reinforcement bars with a 30mm “cover” from the edge.
- If possible use a poker vibrator to eliminate air bubbles, especially when casting foundations. This should be placed vertically to the full depth of the concrete for 15 seconds, then withdrawn slowly and repeated at intervals of 150-250mm across the surface.
- Ensure adequate curing - this is one of the most important aspects to making strong concrete, but is often bypassed in the field due to lack of water, knowledge or organization. Adequate curing is necessary to keep the process of hydration going as long as possible – the longer the time, the stronger the concrete. This hydration process will stop once the concrete has dried out, resulting a strength of concrete according to the time of curing. Although curing can continue even for years, 7 and 28 days are normally quoted (see graph) – curing should last at least 7 days, if not longer especially in cold weather. Curing involves sprinkling water on the concrete every day as well as covering it, preferably in a shady area. Covering can be done with material like plastic or sacking, but covering in wet sand also works well, as does putting the concrete entirely in water.
Reference manuals, videos, and links
- Concrete poker vibrator (commercial product). Found at Alibaba.com.
- Video: How to mix concrete by hand.
Acknowledgements
- CARE Nederland, Desk Study Resilient WASH systems in drought prone areas. October 2010.