Biogas-fueled pump
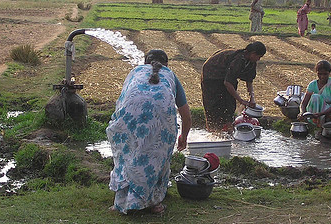
Using biogas for pumps in irrigation is gaining in popularity in India and elsewhere, as the savings in petroleum fuel prices are great. A diesel pump can also be converted into a bio-gas pump used for pumping water. The cheapest way to get biogas, once a pump is obtained, is to build a biomass digester, which means biomass must be collected, cultivated, or found.
Biomass in the form of firewood, charcoal, agricultural residues, or dried animal dung is already the main energy resource for the majority of the poorer half of humanity, over 2 billion people. They currently use 15% or more of total world energy, entirely in the form of biomass. Certain poorer countries depend on biomass fuels at present for over 90% of their energy needs (i.e. mainly for cooking fuel). It has been estimated that 53% of energy use in Africa, 17% in Asia and 8% in Latin America is currently met from biomass resources. Therefore biomass is already a huge and vital economic resource, although it is usually informally exploited mainly for cooking purposes and still remains rarely used for the production of shaft power via heat engines, and even less so for irrigation pumping. However, more and more farmers are using cow dung to create biogas or communities are using toilets to recycle their excrement in their own bio-digesters.
Because biogas digesters have the capability of storing at least a 12-hour supply of gas, an engine can be used that draws gas at quite a high rate. In fact the size of engine is not critical since it is only the number of hours it will run that are governed by the digester gas capacity.
An interesting option for irrigation by biogas power is to combine the digester sludge and the irrigation water in order to perform three functions simultaneously; i.e. irrigation, the application of fertilizer and waste disposal.
Suitable conditions
The main problem with biomass as a fuel is its uneven distribution, being most available in forested regions where it is little needed. Considered as a global resource there is no shortage of biomass, since:
- The world's annual usage rate of energy is only about 10% of the annual natural rate of photosynthetic energy storage (i.e. solar energy stored in plant matter).
- Stored biomass on the earth's surface at present is approximately equivalent to the entire proven fossil fuel reserves (oil, coal and natural gas).
This issue of food versus fuel is an important one, but where the fuel crop is used for irrigation pumping to produce food crops, especially in a small-scale "on-farm" process, the same objections need not apply.
The country which has made by far the most use of biogas production in agriculture is China, where, particularly in Sichuan province, there are several million working biogas units. This development took place almost entirely within the last 10-15 years. The value of the fertilizer output usually surpasses the value of the energy produced by the process in China. The waste disposal and sanitation aspects of the process are also important justifications for its use.
Advantages | Disadvantages |
---|---|
- Makes good use of organic wastes. You can obtain fuel from sewage sludge and animal slurries first, and prevent runoff and methane emissions at the same time – and you still get fertiliser at the end of the process. - Is a clean, easily controlled source of renewable energy. |
- Most practical to be generated and used at the source of the waste. This is because the energy needed to compress the gas for transport, or convert it into electricity is excessive, reducing the efficiency of biogas energy production. - For safety, basic precautions must be adhered to. |
Construction, operations and maintenance
To get biogas, farmers are creating their own, by using cow dung and building a bio-digester. The end products are also a good source of fertilizer for crops. Making their own biogas saves hundreds of US$ per year in fuel costs for fuel that is used to run small water pumps.
The whole biogas (production) process can be divided into three steps: hydrolysis, acidification, and methane formation.
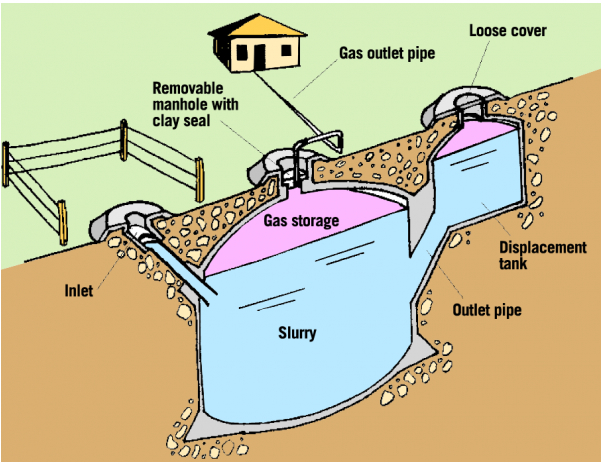
Costs
Cost of bio-digesters:
The flexible balloon installations are relatively cheap (30-100 US$), but are liable to damage. Floating drum and fixed dome digesters are more expensive (700-1200 US$), but are more robust. Floating drum installations are effective, providing gas with a fixed pressure, which is good for domestic use, but can be more expensive and less robust than a fixed dome digester. Fixed dome digesters are more robust as they use no moving parts and can be constructed from local materials.
Manuals, videos, and links
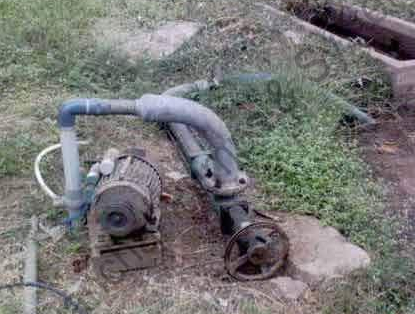
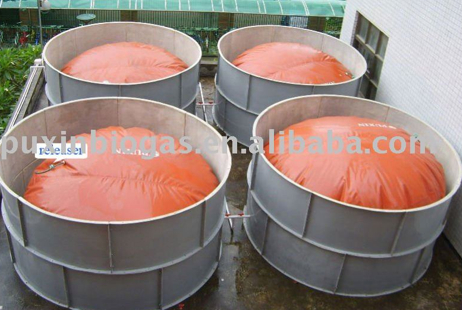
- Article: Biomass Energy in Jordan.
- Instructions: National Bank for Agriculture and Rural Development, Bio-Gas.
- 11 instruction manuals on how to build biogas digesters. from Practical Action.
- Video: Biogas plant construction in Kampala, Uganda.
- Video: Anaerobic methane digester how to, including biogas scrubbing.
- Video: Biogas: how it works.
South Asia
- Video: Purushottam Patel's biogas-driven irrigation pump - A video case study.
- Video: Biogas Driven Irrigation Pump. The diesel pump has been converted to a Biogas driven pump by the farmer, Purushottambhai Patel. Purushottambhai is from Shekhadi village in Petlad Taluka, Anand District (Gujarat). English subtitles.
- Video: Developing Biogas Plant.wmv in Polasong and Belguri village Kamrup district, Assam, INDIA, geographical coordinates N26 06.441 E92 04.290. The soil type is sandy loam to clay.
- Video: KITCHEN WASTE TO BIOGAS - BENEFICIARY STATEMENT. Biotech-India.org
- Video: Biogas project of Bangladesh. The success & problems of Bio gas project in Bangladesh. Not in English.
- Video: Bio Gas in Nepal. The biogas initiative in Nepal. In English and with English subtitles in some sections.
- Video: Biogas-powered Electrictal Generator in Myanmar. Brief video shot at the Myanmar Baptist Convention agricultural training center near Yangon in early March. Biogas brewed from wastes produced by a few hogs located just above this location is piped to an electric generator. Each day, there's enough biogas produced to power the 3 kw generator for 45 minutes in the morning and another 45 minutes in the evening. The generator, in turn, powers lights as well as an electric pump that extracts water from the center's well for storage in an elevated tank. The stored water flows by gravity to spigots throughout the farm. Saw Hei Moo, who directs the project, estimates that the biogas system costs about $350 with the generator running around $300. Toss in perhaps another $100 for pipe, cylinders and other types of essential apparatus.
- Video: Efficient Biogas digesters built by Wasandi BioSolar Company. Wasandi Biosolar (Pvt) Ltd makes Biogas digesters, and has worked for the last few years on making effiecient Biogas digesters. This type of digester is much cheaper to build, lasts longer, easier to repair, gives more gas, and can be built in 2 to 3 days at any place. We gaurantee our digesters for ten years, but our digesters will be good and working for more then 30 to 40 years. Biogas is the cleanest fuel available. If you are intrested in getting Biogas for your home or village, we can make a digester of any size. For details visit our web site: www.wasandi.com
Acknowledgements
- DIY Methane Generator.
- BIOMASS AND COAL (THE NON-PETROLEUM FUELS) FAO.
- Poo power: cow dung can be used as fuel. Practical Action.
- Dr J.U. Smith, The Potential of Small-Scale Biogas Digesters to Alleviate Poverty and Improve Long Term Sustainability of Ecosystem Services in Sub-Saharan Africa. University of Aberdeen, Institute of Biological and Environmental Science.