Difference between revisions of "Centrifugal pump"
(→Reference manuals, videos, and links) |
|||
Line 2: | Line 2: | ||
[[Image:centrifugal pump.jpg|thumb|right|300px|General components of a Centrifugal Pump. Photo: [http://www.maintenanceworld.com/articles/engresource/centrifugalpumps.pdf The Chemical Engineers’ Resource Page]]] | [[Image:centrifugal pump.jpg|thumb|right|300px|General components of a Centrifugal Pump. Photo: [http://www.maintenanceworld.com/articles/engresource/centrifugalpumps.pdf The Chemical Engineers’ Resource Page]]] | ||
[[Image:CentrifugalPump.jpg|thumb|right|300px|Centrifugal pump. <br> Photo: WHO.]] | [[Image:CentrifugalPump.jpg|thumb|right|300px|Centrifugal pump. <br> Photo: WHO.]] | ||
− | + | __NOTOC__ | |
The essential components of a centrifugal pump are the fast-rotating impeller and the casing. Water flows into the centre “eye” of the impeller, where centrifugal force pushes the water outwards, to the casing. The kinetic energy of the water is partly converted to useful pressure that forces the water into the delivery pipe. Water leaving the central eye of the impeller creates a suction, which draws water from the source into the pump. An impeller and the matching section of the casing is called a “stage”. | The essential components of a centrifugal pump are the fast-rotating impeller and the casing. Water flows into the centre “eye” of the impeller, where centrifugal force pushes the water outwards, to the casing. The kinetic energy of the water is partly converted to useful pressure that forces the water into the delivery pipe. Water leaving the central eye of the impeller creates a suction, which draws water from the source into the pump. An impeller and the matching section of the casing is called a “stage”. | ||
Revision as of 04:13, 13 December 2012
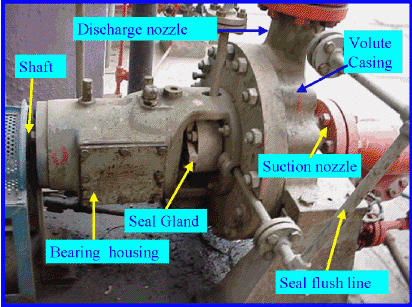
The essential components of a centrifugal pump are the fast-rotating impeller and the casing. Water flows into the centre “eye” of the impeller, where centrifugal force pushes the water outwards, to the casing. The kinetic energy of the water is partly converted to useful pressure that forces the water into the delivery pipe. Water leaving the central eye of the impeller creates a suction, which draws water from the source into the pump. An impeller and the matching section of the casing is called a “stage”.
Several stages can be combined with a single shaft to increase the overall pressure (multiple-stage pump). The water passes through the successive stages, with an increase in pressure at each stage. Multiple-stage centrifugal pumps are normally used when water has to be pumped to a significant height (200 m or more). For deep-well applications, the centrifugal pump and electrical engine are housed in a single unit. When the unit is to be located under the water level, a submersible pump will be required.
Suitable conditions
One limitation of a centrifugal pump is that the suction height cannot be higher than about 7 m above the water level. To overcome this limitation, and make it possible to place the pump above the suction limit, some pumps inject a jet stream of water into the suction pipe inlet. The kinetic energy of the injected water is partly converted into extra pressure, which helps to lift the water above the suction limit of the pump.
Centrifugal pumps are not energy-efficient, especially in the smaller size ranges (that are most common for rural water supply applications). Centrifugal pumps are still used for solar pumping but as electronics have become cheaper and more sophisticated, progressive cavity pumps have become more common. It is not unusual for a centrifugal pump to be found to be oversized, having been poorly selected for its intended duty. This causes a significant waste of energy. In general, centrifugal pumps with inverters and AC motors have efficiencies of 20 to 40%.
Construction, operations and maintenance
Head range: Typically, 4–50 m per stage, with multiple-stage pumps to 200 m and more.
Yield: Varies widely, according to many options available in the market.
Area of use: Anywhere engine power is available.
Trademarks: Grundfos; Drysale; Sta-rite; and others.
During pumping, the condition of the engine, the water output of the pump, and the temperature of bearings should be checked, and any vibration should be reported. In some systems, valves must be closed manually just before switching off the pump, to retain water in the system. Most centrifugal pumps are not self-priming, and if the pump house runs dry, clean water has to be poured into it. The pump inlet should be maintained, and the pump and engine kept clean. A record of the pump running hours, problems, servicing, maintenance and repairs should be kept in a logbook.
The pump should be dismantled annually, and the rising main removed from the well and inspected. The inlet screen, foot valve and pipe threads should be checked, and any corroded or damaged threads re-cut. Badly corroded pipes should be replaced. The foot valve may need a new rubber, or it may have to be replaced. All other repairs, such as replacing the bearings or the impeller, are costly and should be carried out by qualified technicians.
For several reasons, centrifugal pumps are not suitable for village-level maintenance. Pump maintenance requires an organization that focuses on the training and reliability of the pump caretaker, and on raising funds to support the pump O&M. In the event of breakdown, the pump committee must be able to mobilize a trained area mechanic quickly. Centrifugal pumps are designed for specific ranges of flow and pressure, and it is important that pump characteristics and operating conditions are matched by someone properly trained. The starting torque of a centrifugal pump is relatively low, which is an advantage for windmill and solar power applications.
Potential problems
— debris, sand or other particles may enter the pump, causing abrasion damage;
— an inlet becomes clogged, causing cavitation;
— the pipeline system is damaged by severe surges in water pressure, caused by starting and stopping the pump abruptly;
— the pump and engine are badly aligned, causing the bearings to wear out quickly;
— the main limitations of a centrifugal pump are its cost, the need to ensure a reliable supply of electricity or fuel, and the need for skilled technicians to maintain and repair the pump.
Costs
Highly dependent on the power rating and quality of the pump.
Field experiences
Manuals, videos, and links
Acknowledgements
- Brikke, François, and Bredero, Maarten. Linking technology choice with operation and maintenance in the context of community water supply and sanitation: A reference document for planners and project staff. World Health Organization and IRC Water and Sanitation Centre. Geneva, Switzerland 2003.
- WASH Technology Information Packages – for UNICEF WASH Programme and Supply Personnel. UNICEF, 2010.